E-Mail:sales@whalescnc.com
E-Mail:sales@whalescnc.com
Methods for Machining Negative Angle Surfaces on 3-Axis CNC Machine Tools
Abstract
This article addresses the widespread use of 3-axis CNC machine tools and UG NX automatic programming in small and medium-sized enterprises. Through practical examples, we discuss methods for machining negative angle surfaces in cavities using 3-axis CNC machine tools with UG NX. These methods significantly improve production efficiency, ensure surface quality, reduce machining costs, and shorten production cycles.
1. Introduction
In mold manufacturing, negative angle surfaces often appear (see Figure 1). When machining these surfaces using 3-axis CNC machine tools, there are blind spots in the manufacturing process that fail to meet standards. This article explores methods for machining negative angle surfaces using 3-axis CNC machine tools with UG NX.
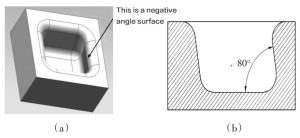
2. Methods for Machining Negative Angle Surfaces
(1) Using a 3-axis CNC milling machine with fixtures.
3-axis CNC milling machines have only three orthogonal axes (X, Y, Z). When using UG NX for contour machining and area milling, there are blind spots in the machining process (see Figure 2). Special fixtures must be designed for secondary clamping to machine negative angle surfaces.
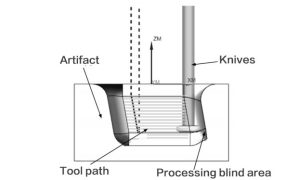
(2) Using Electrical Discharge Machining (EDM).
In EDM, a tool electrode moves relative to the workpiece, replicating its shape and dimensions on the workpiece. During machining, the tool electrode and workpiece are connected to the two poles of a pulse power supply and submerged in a working fluid. Sparks are generated when the gap between the two electrodes reaches a certain distance.
(3) Using a 5-axis CNC machine tool.
5-axis CNC machine tools have X, Y, Z, and any two rotating axes. Compared to traditional 3-axis machining centers, 5-axis centers can quickly and effectively machine negative angle surfaces. They are particularly efficient and high-quality when machining complex geometric shapes.
(4) Using UG NX for surface milling on a 3-axis CNC machine tool.
UG NX surface milling uses a projection method, imagining a light source projecting the machining surface onto a set body, thereby generating a toolpath to meet the requirements for machining negative angle surfaces.
3 Method of Machining Negative-Angle Surfaces using UG NX on a 3-axis CNC Machine
3.1 Tool Creation
When using a 3-axis CNC machine to machine negative-angle surfaces, a round corner face mill is needed. The tool size can be adjusted as required (see Figure 3 for the tool creation page and Figure 4 for the tool parameters used in this article).
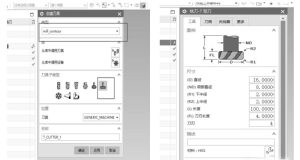
3.2 Creating the Projection Body
The size of the projection body is a crucial parameter in determining the direction, height, and position of the milling area (see Figure 5). After generating the toolpath, you can adjust the size of the projection body to change and optimize the toolpath.
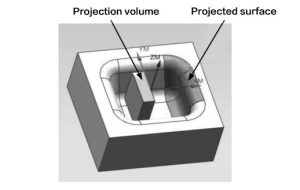
3.3 Creating the Surface Milling CNC Program
- Enter the UG NX machining interface and create a contour milling operation for the surface area (see Figure 6).
- Set the check body: This is a safety measure to prevent over-cutting, which could result in workpiece scrapping (see Figure 6).
- Select the milling area: Choose the specific part and directly select the negative-angle surface that needs to be milled (see Figure 6).
- Choose the driving method: Surface driven; Projected vector: Towards the driving body (see Figure 6).
- Edit the driving method: Specify the driving geometry (i.e., the created projection body seen in Figure 5) as well as milling direction and step (see Figure 7).
Figure 6 Create contour milling process/Figure 7 Create milling direction and step distance - Set the cutting parameters and non-cutting movement parameters.
- Generate the toolpath (see Figure 8). After generating the toolpath, adjust the projection body to meet the workpiece requirements.
Figure 8 Generate tool path - Perform 3D simulation: Use a 3D simulation program to check for issues like over-cutting, tool collision, and excessive milling residue (see Figure 9).
- Post-process to generate the NC machining program (see Figure 10).
Figure 9 Effect of milling and forming after 3D simulation / Figure 10 Generated NC post-processing program
4. Conclusion
Through practical experience and considering that many small and medium-sized enterprises do not have EDM or 5-axis CNC machine tools, we have created a comparison table of the advantages and disadvantages of various machining methods, as shown in Table 1.
Table 1: Processing Service Price List | |||
Service | Specification | Description | Price Range |
3-axis CNC milling | Precision parts | High precision surface processing, good finish | 100-150 RMB/hour |
Electrical Discharge Machining (EDM) | Standard processing | High precision mold processing | 150-200 RMB/hour |
5-axis CNC milling | Standard processing | Precision processing | 200-300 RMB/hour |
3-axis CNC milling | Modeling, UGNX software application | Modeling and processing, complete set of services | 100-150 RMB/hour |
Comparing the data in the table, it is concluded that in actual machining applications, NG NX surface machining has solved the problem of needing special fixtures for machining negative angle surfaces on 3-axis CNC machine tools. By optimizing the machining program, CNC machine tools can more quickly meet workpiece requirements, reducing machining time in manufacturing. It also minimizes the loss of precision caused by secondary clamping, saves on machining costs, and shortens the production cycle.
Keywords
3-axis CNC machine tool
UG NX automatic programming
Cavity
Negative angle surface
Need to buy a machine tool?
You can upload drawings of machined parts. Our experts will help you determine the best machine for your needs.
About WhalesCNC
WhalesCNC is a high-quality CNC machine tool manufacturer located in Xuzhou, Jiangsu, China. It has more than 20 years of manufacturing experience and is committed to comprehensive solutions to improve cutting efficiency.