E-Mail:sales@whalescnc.com
E-Mail:sales@whalescnc.com
Components for CNC machining centers
The Evolution and Impact of CNC Machining Centers
The advent of CNC machining centers has marked a transformative era in the realm of manufacturing. These centers, equipped with the ability to automate and precisely control machining tasks, have become essential in a myriad of industries, from aerospace to medical device production. The significance of CNC technology lies in its versatility and efficiency, enabling the production of complex parts with minimal human intervention.
Exploring the Heart of CNC Precision
This article aims to delve deep into the components of CNC machines. We will navigate through the intricate network of parts that constitute a CNC machining center, understanding how each contributes to the machine’s cutting-edge performance. From the spindle that holds the cutting tool to the sophisticated Machining Centers that manage the entire operation, every component is a cog in a well-oiled machine, driving the industry forward.
As we embark on this journey, we will uncover the functions and intricacies of the components of CNC milling machines—the building blocks that enable the creation of precision parts that are integral to our daily lives.
Ⅰ.Overview of CNC Machining Centers
Defining CNC Machining Centers
At their core, CNC machining centers are automated machine tools that are capable of performing various machining operations with high precision and minimal human oversight. These centers are driven by computer numerical control (CNC), which allows for the programming of complex and intricate tasks. The operational principles of these machines hinge on the conversion of digital blueprints into physical parts through a subtractive manufacturing process, carving out the desired shape from solid blocks of material.
The Journey from Manual to CNC Machining
The historical context of machining centers is a testament to human ingenuity and the relentless pursuit of efficiency. The evolution began with manual machine tools, which required operators to manually guide the cutting tools. The technological leap to CNC machining introduced a new era where machines could be programmed to perform tasks repetitively with unparalleled accuracy. This evolution has been marked by milestones such as the introduction of the first NC (Numerical Control) machines in the 1940s and the subsequent development of CNC technology, which has become more sophisticated with each passing decade.
As we trace the technological evolution of machining centers, we witness a consistent trend towards increased automation, precision, and capabilities. Modern machining centers are equipped with advanced features such as Auto Tool Changers and multi-axis movement, which have expanded the possibilities of what can be manufactured, reducing the time and cost associated with producing complex parts.
In the next section, we will explore the different types of CNC machining centers and how they cater to the diverse needs of the manufacturing industry.
Ⅱ.Main Types of CNC Machining Centers
Vertical Machining Centers (VMC)
Vertical Machining Centers are characterized by a vertically oriented spindle, allowing tools to approach workpieces perpendicularly. This design is advantageous for die sinking work, where the gravity aids in the removal of metal chips. VMCs are typically preferred for their ease of setup and suitability for plate work. They are commonly used in milling, drilling, and tapping operations, making them a versatile choice for manufacturers.
Horizontal Machining Centers (HMC)
In contrast, Horizontal Machining Centers feature a horizontally oriented spindle. This configuration enables the use of a rotary table and can facilitate the machining of multiple sides of a workpiece simultaneously. HMCs are often chosen for jobs requiring heavy cutting loads, such as machining castings and forgings. Their design allows for better chip evacuation, reducing the potential for thermal distortion and improving tool life.
Universal Machining Centers (UMC)
Expanding the capabilities of CNC machining, Universal Machining Centers offer a high degree of flexibility. These machines combine the benefits of both vertical and horizontal machining centers with additional rotational axes that allow for 5-sided (3+2) machining or full 5-axis contouring. This versatility makes UMCs ideal for complex geometries and precision parts, such as those required in the aerospace and medical industries.
Each type of CNC machining center is designed to meet specific manufacturing needs. The choice between a VMC, HMC, or UMC will depend on the particular applications, desired precision, and production volume. As we continue, we will delve into the specific components of CNC machines that enable these advanced capabilities.
Ⅲ.Key Components of CNC Machining Centers
The Control System
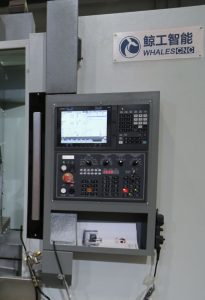
Control Panel
The control panel is the interface where the machinist inputs commands and monitors the CNC machine. It is the direct line of communication between the operator and the machine, featuring buttons, switches, and screens that allow for the precise control of the machining process.
Input Devices
Input devices are the conduits for transferring programming instructions to the CNC machinery. These can range from traditional punch tape readers to modern USB ports and network connections, facilitating the transfer of complex design files directly into the machine’s control unit.
Machine Control Unit (MCU)
At the heart of the control system is the Machine Control Unit (MCU). This sophisticated computer interprets the input data and converts it into mechanical movements, orchestrating the machining process with meticulous precision.
Feedback Systems
Integral to maintaining accuracy, feedback systems consist of sensors and transducers that relay real-time information back to the MCU. This feedback allows for dynamic adjustments during operation, ensuring the highest levels of precision and quality.
The Machine System
Drive System
The drive system includes motors and lead screws that translate the MCU’s commands into movement. This system is responsible for the accurate positioning of the spindle and workpiece, which is critical for the machining operation.
Cutting Tools and Spindle
Cutting tools are mounted on the spindle, which is the rotating axis of the machine. The spindle’s speed and torque are crucial factors in the cutting process, affecting the quality and efficiency of the machining.
Tool Turret
The tool turret holds multiple cutting tools and enables the Auto Tool Changer to quickly switch between tools, minimizing downtime and maximizing productivity.
Machine Bed
The machine bed is the foundation of the CNC machine. It provides stability and support for all components, ensuring that vibrations and external forces do not affect the machining process.
Cooling System
Lastly, the cooling system circulates coolant to manage the heat generated during machining. This system is essential for maintaining the longevity of the cutting tools and the integrity of the workpiece.
Each of these components plays a vital role in the operation of CNC machining centers. In the next section, we will explore the additional functional components that enhance the capabilities of these sophisticated machines.
Section 4: Core Functional Components of Machining Centers
Automatic Tool Changer (ATC) Systems
The Automatic Tool Changer (ATC) is a pivotal component in modern CNC machining centers. It allows the machine to operate with minimal manual intervention, enhancing efficiency and reducing cycle times. The ATC system stores multiple tools in a magazine, enabling the machine to select and change tools automatically during the machining process without operator assistance.
Automatic Pallet Changer (APC) Systems
Similarly, Automatic Pallet Changer (APC) systems contribute significantly to reducing non-productive time. The APC system swiftly exchanges the workpiece-holding pallets in and out of the machining area. This allows for one workpiece to be machined while another is being loaded or unloaded, thus optimizing workflow and increasing machine utilization.
Spindle and Tool Holding Systems
The spindle is the rotating axis that holds and drives the cutting tools. It is a critical component that determines the speed and torque available for cutting operations. Attached to the spindle, the tool holding systems are responsible for securing the cutting tools. These systems must ensure a firm grip to prevent tool slippage and vibration, which could compromise the machining accuracy.
Cooling and Chip Disposal Systems
Effective cooling systems are essential to dissipate the heat generated during machining, protecting both the workpiece and the tools from thermal damage. Coolants also help in flushing away chips from the cutting area, maintaining a clean work environment. In conjunction with cooling, chip disposal systems are employed to manage and remove the byproducts of the machining process, keeping the machine clean and preventing any interference with operations.
These core functional components are integral to the performance and reliability of CNC machining centers. They work in concert to ensure that the machining process is smooth, efficient, and capable of producing parts with the required precision.
In the following sections, we will examine the materials and capabilities that these components support and the applications they enable across various industries.
Need to buy a machine tool?
You can upload drawings of machined parts. Our experts will help you determine the best machine for your needs.
About WhalesCNC
WhalesCNC is a high-quality CNC machine tool manufacturer located in Xuzhou, Jiangsu, China. It has more than 20 years of manufacturing experience and is committed to comprehensive solutions to improve cutting efficiency.